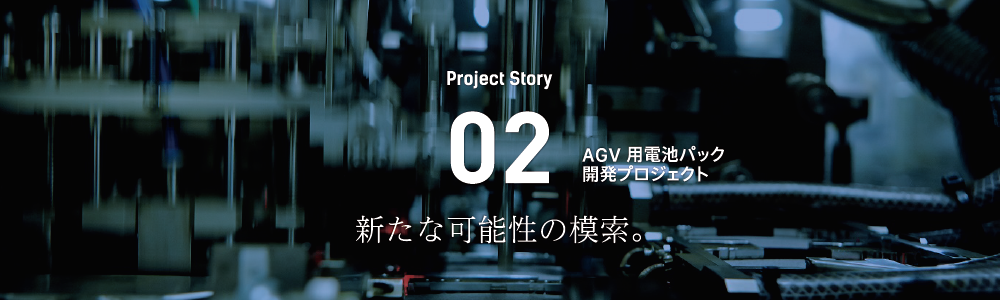
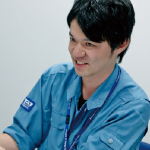
第2技術部
鈴木 隆太郎
鈴木 隆太郎
電池パックの構造設計・機構設計を担当。
“フィン”を用いた間接冷却システムを開発。
“フィン”を用いた間接冷却システムを開発。

ハイブリッド車用に開発された電池をAGVに
適合させるための開発期間は、わずか2カ月。
工場では、様々な搬送車両が活用されている。フォークリフトや台車が代表的だが、その中に、制御プログラムに従って床面に敷設された磁気テープの上を無人で動き、生産現場の効率化に貢献している搬送車両がある。AGV(Automated Guided Vehicle)だ。
2012年秋、お客様から、従来 鉛蓄電池を使用しているAGVの電源を、ハイブリッド車用に開発されたニッケル水素電池に置き換える計画が発案された。
しかしながら、AGVとハイブリッド車では、電池にかかる負荷、電池の使われ方が異なるだけでなく、電池を使用する環境が大きく異なる。ハイブリッド車に搭載される電池パックには、ECU(Electronic Control Unit)やブロアーをはじめとした、電池を冷却するためのシステムが組み込まれている。対して、新規で開発予定のAGV用の電池パックには、スペース、コストといった観点から、同様の冷却システムを搭載することができない。単純に電池を置き換えただけでは、電池が50℃を超える温度まで発熱してしまい、本来の性能を発揮できなくなってしまう可能性があった。解析した結果、電池をAGVに搭載するには、電池の温度を35.8℃未満に抑えなければならないことが分かった。
冷却システム抜きでハイブリッド車用に開発された電池をAGVに適合させる。この難題に挑んだのが、機構設計を担当する入社3年目の鈴木隆太郎だった。
鈴木がプロジェクトの担当に任命された段階で、4カ月後には新型AGVを納品することが決まっていた。この内、わずか2カ月という限られた開発期間で、冷却システム抜きに電池の温度を35.8℃まで抑え込まなければならなかった。それは、ハイブリッド車用に開発された電池を、電池開発ではなく、電池パック開発によって転用するという、新たな可能性を模索する取り組みだった。
2012年秋、お客様から、従来 鉛蓄電池を使用しているAGVの電源を、ハイブリッド車用に開発されたニッケル水素電池に置き換える計画が発案された。
しかしながら、AGVとハイブリッド車では、電池にかかる負荷、電池の使われ方が異なるだけでなく、電池を使用する環境が大きく異なる。ハイブリッド車に搭載される電池パックには、ECU(Electronic Control Unit)やブロアーをはじめとした、電池を冷却するためのシステムが組み込まれている。対して、新規で開発予定のAGV用の電池パックには、スペース、コストといった観点から、同様の冷却システムを搭載することができない。単純に電池を置き換えただけでは、電池が50℃を超える温度まで発熱してしまい、本来の性能を発揮できなくなってしまう可能性があった。解析した結果、電池をAGVに搭載するには、電池の温度を35.8℃未満に抑えなければならないことが分かった。
冷却システム抜きでハイブリッド車用に開発された電池をAGVに適合させる。この難題に挑んだのが、機構設計を担当する入社3年目の鈴木隆太郎だった。
鈴木がプロジェクトの担当に任命された段階で、4カ月後には新型AGVを納品することが決まっていた。この内、わずか2カ月という限られた開発期間で、冷却システム抜きに電池の温度を35.8℃まで抑え込まなければならなかった。それは、ハイブリッド車用に開発された電池を、電池開発ではなく、電池パック開発によって転用するという、新たな可能性を模索する取り組みだった。


50℃を超えて上昇を続ける熱。
解決のカギは、高度な解析技術がもたらした。
従来の鉛蓄電池を置き換える計画が持ち上がったのにはワケがある。ハイブリッド車用ニッケル水素電池は、鉛蓄電池と比べて長寿命化・急速充電使用を可能とする。しかし、そこには課題があった。ニッケル水素電池は充電の際に熱を発するが、急速充電によってより多くの熱が発生してしまうのだ。加えて、温度が上がると電気が流れやすくなり、さらに温度が上がるという性質を持っている。これが繰り返され、高熱になることで電池の劣化が促進されてしまうのだ。
「温度上昇を抑制するために、ハイブリッド車用の電池パックには空気を送って電池を冷却するシステムが搭載されています。ところが、AGV用の電池パックには、それを搭載するスペースがない。そうすると、温度は上がり放題で、50℃を超えてしまうことが分かりました。全く別の方法で電池の温度を下げる仕組みを考える必要があったのです。」
そこで鈴木は、以前から興味を持って取り組んでいた熱流体解析シミュレーション(CFD)を活用し、AGVに搭載された電池が、どの箇所で、どれくらい熱を発しているのかを見える化した。そして、熱問題のメカニズムを解き明かし、問題解決への方策を検討していった。
その末にたどり着いたのが、隣接する電池と電池の間に“フィン”と呼ばれる金属製の板をはさみ込む仕組みだった。
「発想を『冷やす』から『逃がす』に転換したのです。初めて設計した部品だったので不安はありましたが、試作品による試験結果は良好。熱問題にメドが立ち、プロジェクトは大きく前進しました。」
「温度上昇を抑制するために、ハイブリッド車用の電池パックには空気を送って電池を冷却するシステムが搭載されています。ところが、AGV用の電池パックには、それを搭載するスペースがない。そうすると、温度は上がり放題で、50℃を超えてしまうことが分かりました。全く別の方法で電池の温度を下げる仕組みを考える必要があったのです。」
そこで鈴木は、以前から興味を持って取り組んでいた熱流体解析シミュレーション(CFD)を活用し、AGVに搭載された電池が、どの箇所で、どれくらい熱を発しているのかを見える化した。そして、熱問題のメカニズムを解き明かし、問題解決への方策を検討していった。
その末にたどり着いたのが、隣接する電池と電池の間に“フィン”と呼ばれる金属製の板をはさみ込む仕組みだった。
「発想を『冷やす』から『逃がす』に転換したのです。初めて設計した部品だったので不安はありましたが、試作品による試験結果は良好。熱問題にメドが立ち、プロジェクトは大きく前進しました。」
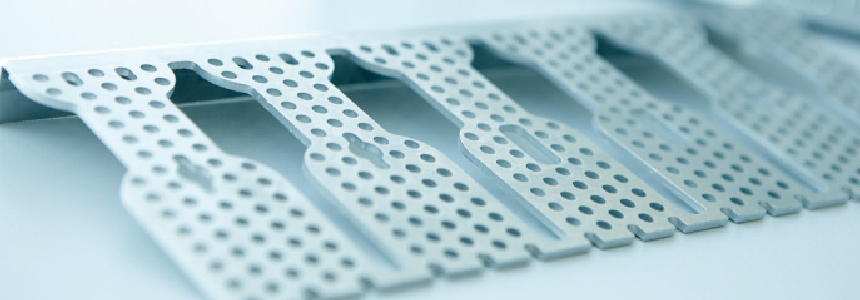

立ちふさがる30mmの壁。
部門を超えた協力で解決策を探し出す。
仕組みは決まった。“フィン”に使う金属も、性能や重量、コストを比較検討した結果、アルミを使うことが決まった。しかし、まだ大きな問題が残っていた。
「開発中の電池パックが所定のスペースを30mmオーバーしてしまったのです。この問題をクリアするには、電池パックを構成する部品をいちから見直さなければなりませんでした。」
電池パックを構成する部品をいちから見直す。これは、部品の形状のみならず、素材や配置 等、すべてを白紙の状態から検討し直すことを意味する。当然、時間もコストもかかる。更に、過去のデータがないため、部品の強度や耐久性など、安全や品質にかかわる性能もいちから評価し直す必要があるのだ。
「とても私一人の力で解決できる問題ではない、そう思いました。そこで、上司に相談のうえ、社内外の関係者に状況を説明し、協力をお願いすることにしました。」
鈴木の声かけに応じ、関係者が動き始めた。材料メーカーからは、新しい電池パックに求められる強度、耐久性を満たす素材の提案があった。その素材を使う想定のもと、鈴木が電池パック全体の設計図を引き直す。そのうえで、社内の強度解析(CAE)を得意とするメンバーがシミュレーションを行った。そして、関係者全員が集まって議論し、材料や部品の大きさについて最適な解を出していった。
「あの時のやりとりは、まさに『プロが集まったモノづくり』でした。各分野の専門家が知恵を持ち寄り、1つの目標に向けて役割を全うしていく。とてつもなく慌ただしい日々でしたが、疲れも感じないぐらい充実した時間でした。」
こうして、AGV用電池パックは完成した。もちろん、完成の期日も予定通りのものだった。
「開発中の電池パックが所定のスペースを30mmオーバーしてしまったのです。この問題をクリアするには、電池パックを構成する部品をいちから見直さなければなりませんでした。」
電池パックを構成する部品をいちから見直す。これは、部品の形状のみならず、素材や配置 等、すべてを白紙の状態から検討し直すことを意味する。当然、時間もコストもかかる。更に、過去のデータがないため、部品の強度や耐久性など、安全や品質にかかわる性能もいちから評価し直す必要があるのだ。
「とても私一人の力で解決できる問題ではない、そう思いました。そこで、上司に相談のうえ、社内外の関係者に状況を説明し、協力をお願いすることにしました。」
鈴木の声かけに応じ、関係者が動き始めた。材料メーカーからは、新しい電池パックに求められる強度、耐久性を満たす素材の提案があった。その素材を使う想定のもと、鈴木が電池パック全体の設計図を引き直す。そのうえで、社内の強度解析(CAE)を得意とするメンバーがシミュレーションを行った。そして、関係者全員が集まって議論し、材料や部品の大きさについて最適な解を出していった。
「あの時のやりとりは、まさに『プロが集まったモノづくり』でした。各分野の専門家が知恵を持ち寄り、1つの目標に向けて役割を全うしていく。とてつもなく慌ただしい日々でしたが、疲れも感じないぐらい充実した時間でした。」
こうして、AGV用電池パックは完成した。もちろん、完成の期日も予定通りのものだった。

私たちの現場

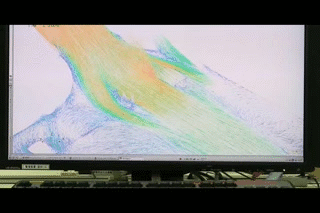
電池パックの熱流体シミュレーション
電池の寿命低下を防ぐためには、電池を所定の温度内かつ均等に冷却することが重要。そのために設計段階でシミュレーションを行い、最適な形状を検討します。
CAEのフル活用とSE活動で設計再検討を撲滅。
スピーディーな生産への移行を実現した。
2カ月で新しい電池パックの設計を完了させる。鈴木によれば、「通常、試作パックの設計だけで4カ月はかかる」とのことであり、これがどれほど異例のスピードかおわかりいただけるだろう。では、そんなにもスピーディーな開発・生産が実現できたのは何故か。
その理由の1つは、鈴木が活用したCFDや社内メンバーが活用したCAEなど、コンピュータを使った解析をフル活用したことにある。鈴木たちは評価試験の前に高精度な解析を行うことで、評価試験の一発クリアを成し遂げたのだ。
もう1つの理由は、社内のサイマルテニアス・エンジニアリング(SE)活動にある。SE活動とは、設計者だけでなく、生産技術部門や製造部門、部品の仕入先の担当者までもが新製品の開発に参画し、それぞれの視点から課題の解決に向けたアイデアを出し合って設計に落とし込むことだ。今回のプロジェクトでも、生産技術の担当者から様々なアイデアがもたらされ、「設計の段階では問題なくても、生産段階で問題が起こる」という事態を未然に防止することができたのだ。
「今回SE活動が力を発揮したのは、活動へ参画する人が皆、他部門の仕事にも深い理解を持っているという、当社ならではの背景があったからだと思います。設計は何に悩みがちなのか、生産技術はどんなことを望んでいるのか、といったことをお互いがよく知っていたのです。」
さらに鈴木は付け加える。「他部門のことが理解しやすいのは、部門間の垣根が低く日頃からコミュニケーションを取りやすい当社の社風があるからです」。他部門のメンバーと、日常の中で何気なく交わされる会話。それを通して相手の仕事や課題への理解を深めていく。もちろん、人とのつながりも同時に深まる。それが業務の場に活かされ、力を発揮したのが今回のプロジェクトなのだ。
その理由の1つは、鈴木が活用したCFDや社内メンバーが活用したCAEなど、コンピュータを使った解析をフル活用したことにある。鈴木たちは評価試験の前に高精度な解析を行うことで、評価試験の一発クリアを成し遂げたのだ。
もう1つの理由は、社内のサイマルテニアス・エンジニアリング(SE)活動にある。SE活動とは、設計者だけでなく、生産技術部門や製造部門、部品の仕入先の担当者までもが新製品の開発に参画し、それぞれの視点から課題の解決に向けたアイデアを出し合って設計に落とし込むことだ。今回のプロジェクトでも、生産技術の担当者から様々なアイデアがもたらされ、「設計の段階では問題なくても、生産段階で問題が起こる」という事態を未然に防止することができたのだ。
「今回SE活動が力を発揮したのは、活動へ参画する人が皆、他部門の仕事にも深い理解を持っているという、当社ならではの背景があったからだと思います。設計は何に悩みがちなのか、生産技術はどんなことを望んでいるのか、といったことをお互いがよく知っていたのです。」
さらに鈴木は付け加える。「他部門のことが理解しやすいのは、部門間の垣根が低く日頃からコミュニケーションを取りやすい当社の社風があるからです」。他部門のメンバーと、日常の中で何気なく交わされる会話。それを通して相手の仕事や課題への理解を深めていく。もちろん、人とのつながりも同時に深まる。それが業務の場に活かされ、力を発揮したのが今回のプロジェクトなのだ。
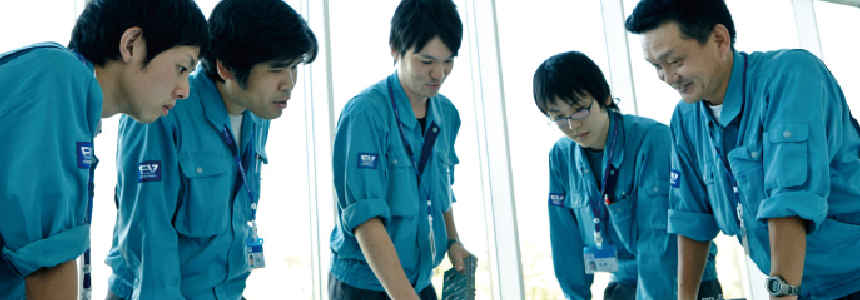

追加注文を受けるほどの好評ぶり。
電池の汎用性を示すことに成功した意味は大きい。
AGV用電池パックは当初、100台分のみ注文を受けていた。それが現在、月に50台ずつの追加注文を受けている。この事実が何よりも、顧客の満足ぶりを雄弁に物語っている。
鈴木たちが開発した“フィン”を用いて冷却するシステムは、小さなスペースでもハイブリッド車用に開発された電池が使えることを実証してみせた。鉛蓄電池の寿命は約3年。対して、ニッケル水素電池を用いた新型電池パックは6年を想定して作られた。電池交換費用の削減によるコスト低減が見込めるため、AGVだけではなく、更に違った用途が広がっていく可能性を示したのだ。
鈴木本人は、解析技術の持つ可能性にこれまで以上に魅了されるようになった。今回のプロジェクトで、熱伝導に関する解析スキルを磨くことができた。次に目指しているのは、強度解析のマスター。そして、電池パック全体を見ながらさまざまな解析を行えるようになることで、「どんな条件でも最適値を見つけられる設計者になりたい」と言う。
鈴木は今、別の案件でもSE活動に携わっている。当然、他部門への理解をさらに深め、協力していくことが求められている。一方では機構設計のスペシャリストを目指しながら、もう一方では、他部門へも精通したゼネラリストを目指す。相反するようだが、これが鈴木の目指す技術者像だ。それは、PEVEの技術者全員が目指す「電池のプロ」という姿にほかならない。
鈴木たちが開発した“フィン”を用いて冷却するシステムは、小さなスペースでもハイブリッド車用に開発された電池が使えることを実証してみせた。鉛蓄電池の寿命は約3年。対して、ニッケル水素電池を用いた新型電池パックは6年を想定して作られた。電池交換費用の削減によるコスト低減が見込めるため、AGVだけではなく、更に違った用途が広がっていく可能性を示したのだ。
鈴木本人は、解析技術の持つ可能性にこれまで以上に魅了されるようになった。今回のプロジェクトで、熱伝導に関する解析スキルを磨くことができた。次に目指しているのは、強度解析のマスター。そして、電池パック全体を見ながらさまざまな解析を行えるようになることで、「どんな条件でも最適値を見つけられる設計者になりたい」と言う。
鈴木は今、別の案件でもSE活動に携わっている。当然、他部門への理解をさらに深め、協力していくことが求められている。一方では機構設計のスペシャリストを目指しながら、もう一方では、他部門へも精通したゼネラリストを目指す。相反するようだが、これが鈴木の目指す技術者像だ。それは、PEVEの技術者全員が目指す「電池のプロ」という姿にほかならない。